【導讀】由于各地政府對汽車尾氣二氧化碳排放的限制越來越嚴格,輕量化是目前汽車制造中最熱門和最重要的話題之一。輕量化可以從結構設計、材料以及工藝三個方面來實現。而這三個方面都需要一種實現的工具:激光。
使用不等厚板是目前最成熟最廣泛應用的的優(yōu)化車身結構設計方法,而不等厚板則是采用的激光拼焊實現的。
輕量化的材料,目前最常用的有熱成型和鋁合金。熱成型材料由于硬度太高,需要激光切孔和修邊;鋁合金焊接的最佳方式也是激光。
而車身零部件之間的連接,采用激光焊接也可以減小法蘭寬度,減輕重量。包括汽車上其他各種部件,如汽車座椅的焊接,也越來越多的采用激光焊接來實現輕量化。
以上所有這些激光加工工藝,TruDisk碟片式激光器都可以完美勝任!
激光拼焊及鋁硅涂層剝除
激光拼焊是汽車車身零部件中較早的激光應用。其優(yōu)點是可以將兩種或者多種厚度的板材拼焊起來,在滿足車身上各個部位的不同強度要求的同時,減輕車身的重量。由于激光拼焊有著悠久的歷史,其使用的激光源也一直在不斷演進。從1980年代的二氧化碳激光器,到2000年后的燈管泵浦固體激光器,直到2006年后開始使用TruDisk激光器。
由于TruDisk碟片激光器轉換效率高(>30%),維護成本低(僅水循環(huán)系統(tǒng)需要維護),較早的激光拼焊線上的二氧化碳激光器和燈管泵浦固體激光器也都已經更換為最新的TruDisk激光器。根據寶鋼的成本核算,更換新激光器的成本,在3年內即可通過節(jié)省使用成本的方式收回投資。
激光拼焊板與熱成型材料都是汽車輕量化的重要技術。兩種技術的結合使用,將不同厚度的鋼板拼焊之后再進行熱成型處理,能夠更進一步優(yōu)化車身的強度分布,從而減輕重量。
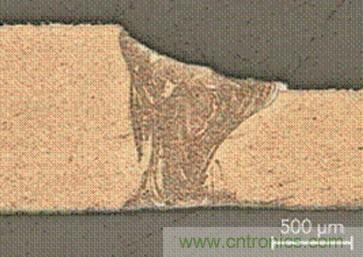
圖1,含鋁硅元素的焊縫
為了防腐蝕,大多數的熱成型材料都有鋁硅涂層。而在激光焊接過程中,鋁硅涂層將在焊縫中形成FeAl合金金相(如圖1所示),從而導致激光焊縫無法通過抗拉強度測試。因而,在激光焊接前必須去除鋁硅涂層。
最常見的鋁硅涂層厚度是20μm(如圖2所示)。而在涂層與母材中間,會形成一層成分為FeAl3 和 Fe2Al5的合金層,其熔點高于鋁硅涂層,達到1000~1100℃。因而在剝除涂層過程中,可以通過精確控制激光工藝參數,保留熔點較高的合金層,以保留零件的防腐蝕新能。
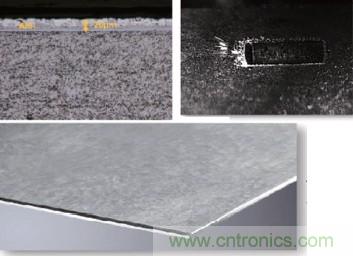
圖2 ,鋁硅涂層被剝除后的鋼板邊緣
這種剝除工業(yè)采用的是一種短脈沖的激光器:TruMicro 7060。其脈沖寬度為納秒量級,最大脈沖能量達80mJ,平均功率為850W。而這種TruMicro激光器也是在碟片激光器平臺上開發(fā)而來的,即在碟片激光器諧振腔內部增加調Q開關來獲得納秒級短脈沖(如圖3所示)。
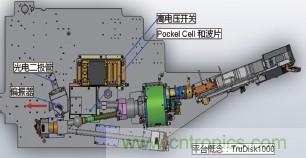
圖3,TruMicro 激光器諧振腔
TruMicro 7060激光器可通過方形光纖和特殊鏡頭,獲得線型光斑,以在涂層剝除時達到更高的能量利用率。這樣,涂層剝除速度可達5cm2/s。也就是說,在剝除1mm的邊緣寬度時,其線速度可達500mm/s,即30m/min。對于拼板焊,兩塊板的兩面都需要進行涂層剝除,這樣,整個工序的剝除速度可達即7.5m/min。這一速度正好與常見的激光拼焊速度匹配。所以這種剝除工藝可以被集成到激光拼焊生產線中,實現完美的在線生產。

圖4,用于激光飛行焊的TruDisk激光器+PFO振鏡
激光飛行焊接
除了激光拼焊,激光飛行焊也已經被廣泛應用于汽車車身及其他零部件的焊接。激光飛行焊是將振鏡焊接頭與機器人的運動結合起來,實現高效靈活的激光焊接。振鏡(PFO)及飛行焊的原理見圖4、5、6。其中PFO可以通過兩片鏡片的旋轉,實現激光焦點在工件上的快速靈活移動和定位,可以大大提供激光焊接時的動態(tài)性能,更加高效。而機器人則可以擴展焊接范圍,以實現更大零件的焊接。兩者的結合,則可以實現優(yōu)勢互補,達到高效、靈活、低成本的激光焊接。
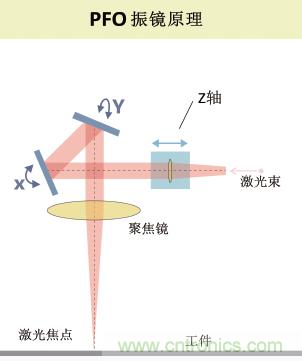
圖5,PFO振鏡原理
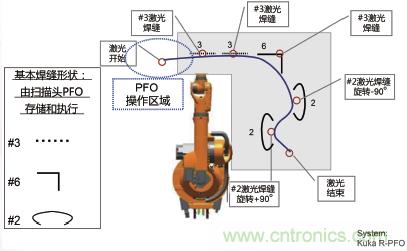
圖6,激光飛行焊原理
相比于傳統(tǒng)的電阻電焊,激光飛行焊接有如下優(yōu)勢:
● 焊接所需法蘭寬度小,可節(jié)省材料,減輕重量;
● 焊縫形狀和方向可以根據零件進行靈活編程設定,以達到最佳的應力分布;
● 由于激光焊縫強度更強,可用更少的焊縫數量達到零件強度要求;
● 生產效率高:激光束從一個焊縫位置跳轉至下一條焊縫位置只需<35ms,基本消除非焊接時間,大大減小生產節(jié)拍,提供生產率,降低單件生產成本。
● 實現相同產能所需設備數量大大減少,減小設備占地面積。
在汽車車身上,激光飛行焊常用于車門、側圍等部件的焊接。例如車門采用激光飛行焊接,可以減小窗框寬度,增大窗戶面積,減輕車門重量,同時提供生產效率。根據奔馳的實際使用經驗,一套激光飛行焊接系統(tǒng)可替代10套電阻電焊。
此外,激光飛行焊也已經在汽車零部件的焊接上廣泛應用,比如汽車座椅部、面板支架等部件的焊接。
三維激光切割
熱成型零件由于硬度高,通過傳統(tǒng)沖壓方式進行沖孔和切邊會導致模具快速損傷,成本非常高。而激光切割則對材料的硬度完全不敏感,目前已經是熱成型生產線中標準的工序。針對這一應用,通快專門開發(fā)了三維五軸激光切割機床TruLaser Cell 8030,其使用的也是TruDisk激光器,最通用的型號是TruDisk 3001,激光功率為3kw。
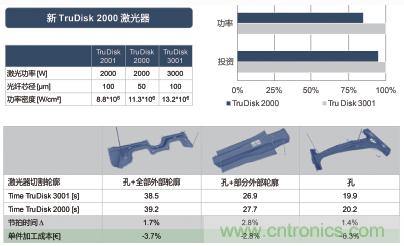
圖7,TruDisk 2000與TruDisk 3001的切割成本對比
為了降低單件加工成本,我們也開發(fā)了采用2kw激光器TruDisk 2000的激光切割工藝。雖TruDisk 2000的激光功率只有TruDisk 3001的2/3,但其功率密度卻非常接近,因為它的光纖更細,芯徑只有50μm。因此,對于一些較薄零件的切割,TruDisk 2000的切割時間只比TruDisk 3001多了2%,而單件加工成本卻最多可以降低6%(圖7),其投資成本和能耗更低。
小結
激光已經成為汽車輕量化所必需的一種工具。由于各種激光的各種特性和優(yōu)勢,其應用將會越來越廣泛。而激光加工的發(fā)展方向必然是更加高效、更加靈活和更低的成本。TruDisk激光器正順應了這一趨勢,從1999 年的第一代碟片激光器, 到最新的6C系列TruDisk激光器,其激光功率越來越高,能耗卻越來越低,體積也越來越小。相信下一代的TruDisk激光器將會有更大的進步。